Exactly How Defoamers Improve Effectiveness in Production and Manufacturing
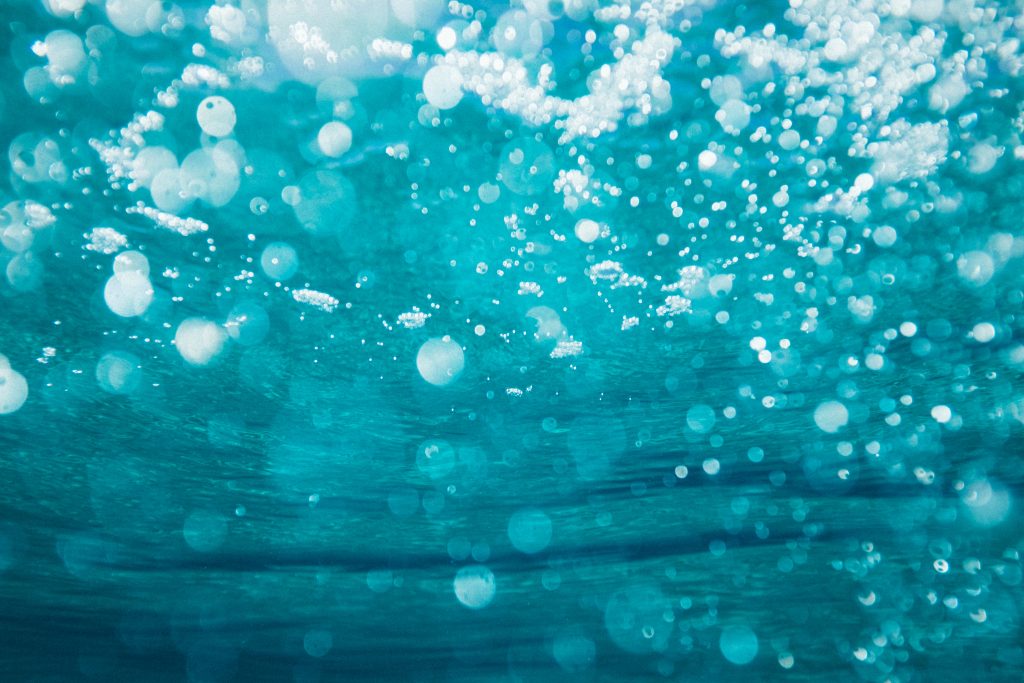
Comprehending Defoamers
Defoamers play an important duty in various manufacturing processes by properly combating the development of foam, which can interrupt procedures and affect item top quality. Foam can develop in countless contexts, such as throughout mixing, home heating, or chemical reactions, potentially causing ineffectiveness and variances in products. The device by which defoamers operate typically entails decreasing the surface area stress of the fluid, enabling bubbles to increase and integrate to the surface area quicker, where they can after that rupture.
Defoamers are developed from a variety of chemical compounds, including natural materials, silicones, and surfactants, each tailored to particular applications and procedures. The choice of defoamer depends on factors such as the type of material being processed, temperature, and the existence of various other additives. Effective defoamers not just minimize foam development yet also keep compatibility with the product, guaranteeing that there are no damaging impacts on the last output. Understanding the buildings and features of defoamers is essential for producers intending to enhance their processes, enhance performance, and maintain the honesty of their products.
Secret Advantages of Defoamers
Utilizing defoamers in manufacturing procedures provides a variety of substantial benefits that boost operational performance and item quality. One of the key advantages is the reduction of foam development during manufacturing, which can obstruct equipment and interfere with operations. By minimizing foam, defoamers make sure smoother procedures, causing reduced downtime and upkeep costs.
Additionally, defoamers boost item consistency by preventing air entrapment, which can endanger the integrity of the last product. This is specifically essential in sectors where visual look and appearance are essential, such as in paints, coverings, and food. Boosted product high quality not only meets customer assumptions yet also enhances brand credibility.
Furthermore, defoamers can aid in maximizing source use. By improving the effectiveness of resources utilization, they add to set you back financial savings and minimized waste, aligning with sustainability objectives. Lastly, the application of defoamers can cause much shorter handling times, enabling producers to boost manufacturing ability without substantial resources investment - defoamers.
Applications in Various Industries
In manufacturing procedures throughout different sectors, the application of defoamers plays an essential function in boosting effectiveness and product quality. These chemical ingredients are utilized in fields such as food and drink, pharmaceuticals, and textiles to mitigate foam-related obstacles.
In the food and beverage market, defoamers are important throughout the fermentation process, preventing foaming that can interfere with production and spoil the product's integrity. In the pharmaceutical sector, defoamers are made use of in the formula of liquid medicines, making certain harmony and security while reducing waste.
Fabric manufacturing additionally gains from defoamers, as they are utilized in coloring and ending up processes to promote even distribution of dyes and chemicals. This application not only improves the end product's look however likewise reduces the amount of water and power eaten throughout production.
Furthermore, in the paper and pulp market, defoamers assist keep process efficiency by reducing foam that can hinder machinery performance. In general, the diverse applications of defoamers throughout these sectors underscore their importance in enhancing production procedures and supplying high-grade products.

Choosing the Right Defoamer
Picking a suitable defoamer is important for taking full advantage of efficiency and top quality in making procedures. The option of defoamer depends upon different factors, consisting of the specific application, the sort of foam being created, and the formulation of the item being made.
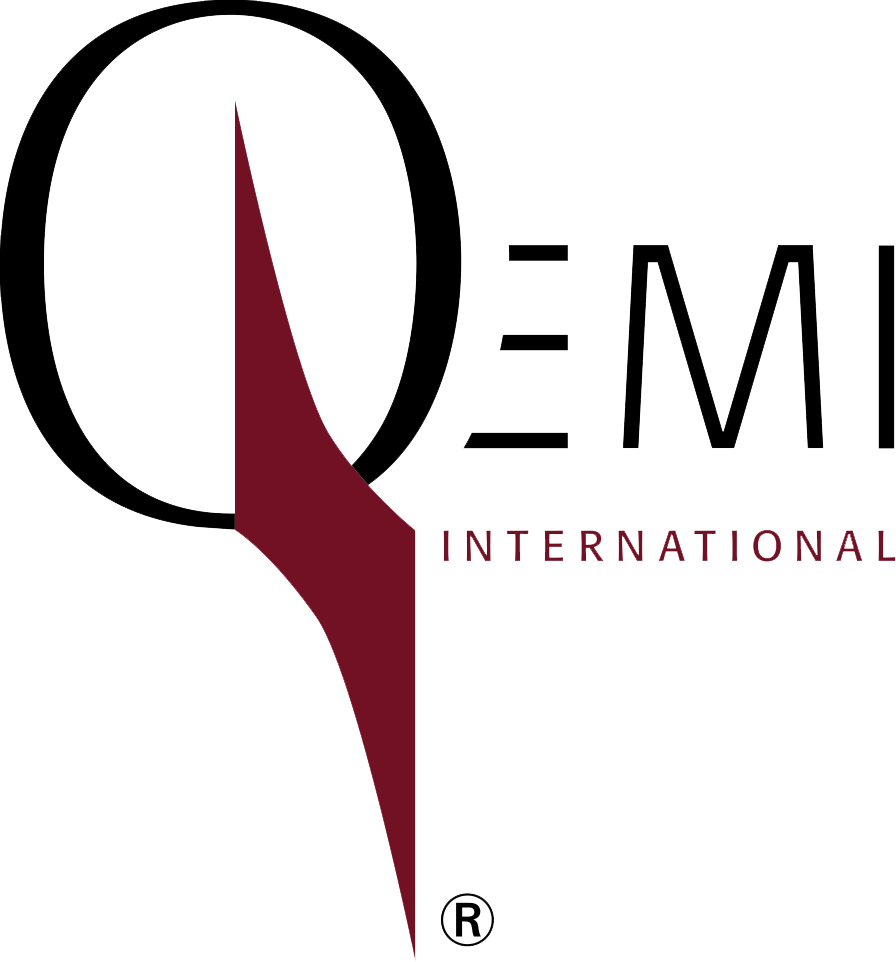
To start with, consider the chemical compatibility of the defoamer with various other ingredients in your formulation. A defoamer that communicates negatively with original site various other components can negatively affect product top quality. In addition, the temperature and pH range throughout processing are essential; some defoamers do efficiently under specific problems while becoming inadequate in others.
Secondly, assess the defoamer's efficiency attributes, such as its capacity to rapidly decrease foam and its perseverance during production. It is vital to read the article choose a product that not only removes foam rapidly however also preserves its efficiency gradually.
Finally, take into consideration regulative and ecological elements, particularly if your production process is subject to strict compliance criteria. Choosing a low-toxicity or eco-friendly defoamer can help satisfy sustainability objectives while guaranteeing operational performance. By attentively evaluating these requirements, suppliers can make informed decisions that boost performance and product integrity.
Ideal Practices for Implementation
Successful implementation of defoamers in manufacturing procedures requires careful planning and adherence to ideal techniques. Choosing the ideal defoamer, as previously discussed, is vital; guarantee it is compatible with the materials entailed and resolves the determined lathering problems efficiently.
Next, keep clear interaction with all stakeholders, including operators and top quality control groups. Training sessions can help make sure that everyone understands the dosing treatments, potential influence on product top quality, and security factors to consider. Carrying out a trial stage can likewise be useful; monitor efficiency closely to determine efficiency and make required changes.
Furthermore, regular screening and tracking of foam degrees can offer valuable understandings right into the defoamer's performance over time. Readjusting dosages in feedback to changes in manufacturing variables will assist maintain ideal efficiency - additional info defoamers. Ultimately, documenting all procedures and results advertises constant renovation, allowing for fine-tuning of defoamer usage and enhancing general performance in producing procedures.
Final Thought
In recap, defoamers play a vital duty in boosting performance within production and manufacturing processes. By lessening foam formation and helping with bubble coalescence, defoamers add to enhanced product high quality, consistency, and operational performance.
The advantages prolong to product high quality and expense savings, as defoamers help streamline processes.Defoamers play a crucial role in numerous making procedures by effectively combating the development of foam, which can disrupt operations and influence product quality. Understanding the residential properties and functions of defoamers is important for manufacturers intending to enhance their processes, boost productivity, and maintain the integrity of their products.
Utilizing defoamers in producing processes provides a variety of significant advantages that enhance operational efficiency and product quality.Furthermore, defoamers enhance product uniformity by protecting against air entrapment, which can jeopardize the integrity of the last product.